European Tech Weekly - Week 9 - 2024 | Industrial Automation
40+ rounds were announced last week with $650m+ flowing into European Tech
Welcome to the latest edition of European Tech Weekly, a newsletter that provides a weekly summary of seed+ funding rounds in Europe. About the author - my name is Chirag Modi, and I am a tech investor based in London.
*** I have recently also started US Tech Weekly. Subscribe here. ***
Funding Announcements in Europe by Stage
Note: Minimum deal size of $1m for seed and $10m for Series A; excludes several sectors such as biotech; non-exhaustive; excludes debt funding
Selected Thematic Clusters
Based on recent fundraising activity in Europe and the US, I aim to identify interesting thematic clusters with increased funding activity. This week, I will provide a 30,000-foot view of industrial automation.
Industrial Automation
Industrial Automation Market Overview
The industrial automation market refers to the equipment and software that regulates, controls and measures an industrial process. In essence, industrial automation systems represent the substitution of labour with capital, driving cost savings and achieving higher productivity. Up to 85% of all assemblies are estimated to be automatable, implying high automation potential. According to McKinsey, “Industrial automation will represent a c.$115bn global market in 2025 (+3.5% annual growth).
Based on end market exposures, the industrial automation market can be segregated into three main categories (McKinsey):
Process automation: Provides automation solutions for continuous manufacturing processes, which typically involve the blending and treatment of raw materials (such as oil & gas, pulp & paper and chemicals) into various products. These industries have been spending the most by far to automate their traditional equipment because their control systems are usually larger and are purchased for considerably longer durations. In total, they will spend about $76 billion in 2025, up from $64 billion in 2019, implying a CAGR of about 2.8%. Key vendors include ABB, Emerson, and Honeywell.
Discrete automation: Provides assembly solutions to manufacturing industries. It involves the assembly of parts to construct products that can be measured in units, such as automobiles, and household appliances. Automation spending is considerably lower in this manufacturing category ($26 billion in 2019) but is growing faster (at a CAGR of about 3.9%), with high variation between sectors. The semiconductor, electronics and electrical sectors are increasing their automation spending the fastest. Key vendors include Siemens, Rockwell Automation, Schneider, ABB and Kuka (Midea).
Industrial IoT and software services for processes and discrete manufacturing (digital segment): This segment includes all the solutions that connect industrial equipment within a factory and enable the use of data analytics and the creation of data-driven supply chains. It is the smallest automation product segment but, at 18%, the fastest growing. A good overview of the various industrial software sub-categories can be found here.
Illustrative Market Map
From an asset/hybrid-light business model perspective, the digital segment is the most relevant. According to a McKinsey survey (Jun-22, 188 US and European participants), 69% of respondents said digital solutions are already an important part of their automation efforts.
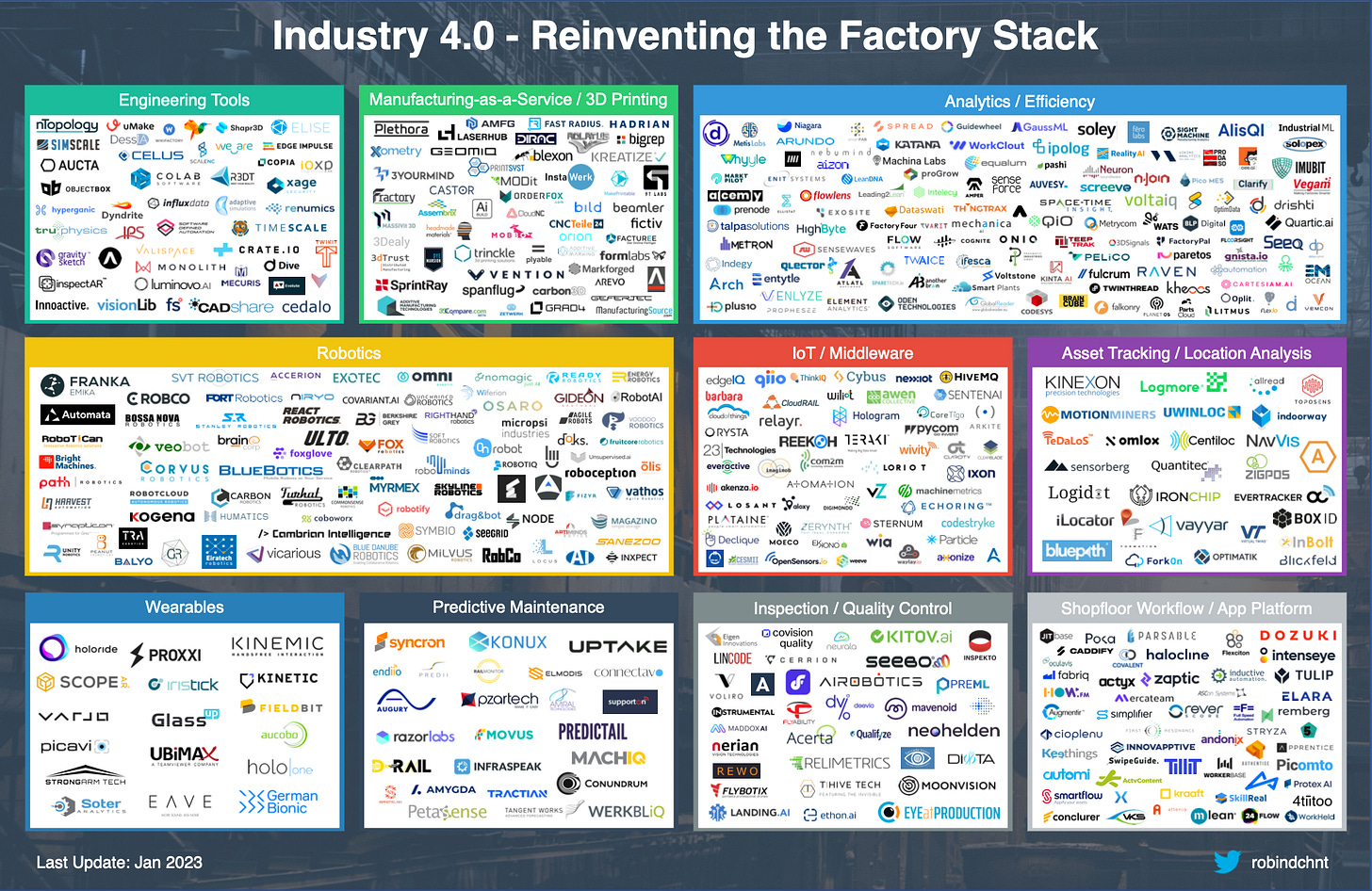
Robin Dechant has put together a helpful market map of 500+ active startups that are reinventing the factory stack. He also runs an informative newsletter on the Future of Manufacturing!
Selected trends
It is worth spending time going through the various categories of the market map. In order to help prioritise any top-down research, I have outlined a few interesting themes:
Teach-less / modular Robotics and Focus on SMBs
“Industrial robots are designed to perform a range of tasks that are too difficult, dangerous, or repetitive for humans. However, such robots are typically built for operation in highly-structured environments with very few unknowns” (Contrary). In general, the robots need to be significantly configured (hardware + software) for specific use cases in factories. According to BCG, “in their standard configuration, they are not good at adjusting to unforeseen events or adapting automatically to variations.” Hence, the level of robotics penetration remains low globally. According to IFR, the worldwide supply of Robotics stands at only 3.9m worldwide.
Various technology advancements (AI, virtual simulation, edge computing, System on a Chip and 5G) enable new automation use cases that incumbents (e.g. Siemens, Rockwell Automation, Fanuc) have not addressed at scale. Hence, there is an automation gap that exists between what is possible with advanced technology today vs. what the incumbents offer. Furthermore, the adoption in the SMB segment is relatively low due to implementation and deployment costs as well as long payback periods.
Teach-less / modular/autonomous robotics usher in an era of smarter robots and cobots that need little training to perform new tasks as well as cost less, potentially also expanding the market to SMBs that lack expertise and training budgets as well as faster integration.
Notable companies: Robco*, Automata*, 1x, Unchained Robotics*, Covariant, Anybotics, Locus, Ambi Robotics, Flink
Emergence of Industrial LLMs
According to Contrary, there are two main approaches to teaching robots how to behave in unstructured environments: hierarchical learning and language-based learning.
Hierarchical learning “builds off of the intuition that any complex task, like washing the dishes, is composed of a series of simpler tasks organized in a hierarchical order. Washing the dishes involves picking up a dish, scrubbing it with soap, rinsing it with water and then drying it in precisely that order.” However, this approach requires a lot of examples to learn, which means large data sets are needed to train them.
Language-based learning “begins with the insight that complex tasks could just as easily be broken down into simpler instructions by a sophisticated language mode.” Deepmind’s Gato and Google’s SayCan are examples of combining LLMs with robots, enabling robots to execute more complex functions.
LLMs are being applied to products and services in the factory stack across the automation process, which can be divided into 3 key stages:
Design & Development: According to Exponential Industry, “LLMs are currently improving the development phase in two distinct ways. One way is the family of “copilots” for robots (e.g. RAPID, TP, INFORM) and CNC (e.g. G-code), etc. The other way is through new ‘foundation models’ designed specifically for industrial applications such as robot picking.”
Deployment phase: “LLMs are currently improving the deployment phase in similar ways to the development phase. Moving to the Level 1/2 layers there are also ‘copilots’ for PLC (Ladder Logic), FactoryTalk, TwinChat, and HMI (Ignition) code generation that orchestrate a process.” (Exponential Industry)
Usage and Maintenance: “LLMs can serve as an intuitive interface for operators to interact with the system, simplifying the process of querying system statuses or troubleshooting issues. LLMs can guide technicians through complex calibration procedures, providing step-by-step instructions and adjusting guidance based on real-time feedback from the system.” (Exponential Industry)
Illustrative use cases: PickGPT (Sereact), Covariant Brain foundation model (Covariant), LLM-based control code generation using image recognition (ABB), MultiPly
The hypothesis that existing automation players will derive substantial benefits from integrating Generative AI into their products and workflows is gaining traction. While it remains to be seen whether new, standalone Generative AI-first automation entities in industrial automation will emerge, the potential for domain-specific foundation models, particularly in robotics, is immense. The main hurdle is access to training data, which is not readily available. However, it is expected that more startups will enter the race to build proprietary data sets of robotic inputs & action outputs for specialized applications.
IoT / Middleware - Simplification and standardization
In the factory stack, the middleware layer enables harmonization of data, standard for data exchanges and orchestration of workflow, increasing the interoperability, and openness of automation systems and/or improving human-robot interactions, enabling scaling of digital use cases across the factory.
However,
Notable companies: Sparetech, Pelico, Wandelbots, HiveMQ, Assemblio*
Further reading
The new industrial tech - NGP Capital
The Future of Manufacturing Newsletter - Robin Dechant
The Rise of Robotics - Contrary
Industrial Intelligence - Activant Capital
Disclaimer
This post and the information presented are intended for informational purposes only. The views expressed herein are the author’s alone and do not constitute an offer to sell, or a recommendation to purchase, or a solicitation of an offer to buy, any security, nor a recommendation for any investment product or service. While certain information contained herein has been obtained from sources believed to be reliable, neither the author nor any of his employers or their affiliates have independently verified this information, and its accuracy and completeness cannot be guaranteed. Accordingly, no representation or warranty, express or implied, is made as to, and no reliance should be placed on, the fairness, accuracy, timeliness or completeness of this information. The author and affiliated persons and companies assume no liability for this information and no obligation to update the information or analysis contained herein in the future.